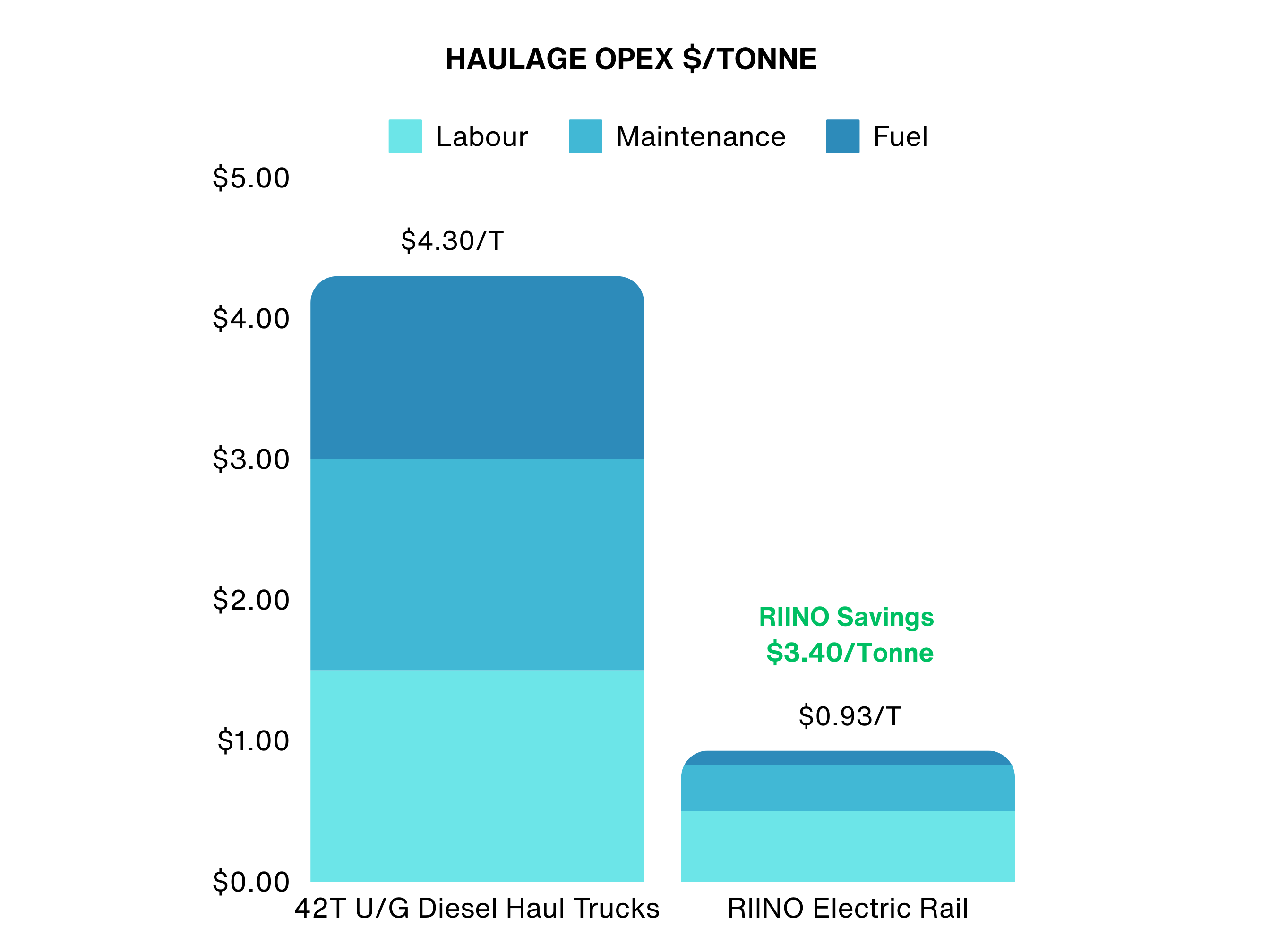
Underground & oPEN-PIT
Lowered Haulage OPEX by
50% - 90%
Rail is the most efficient means of transportation Full electric and automated operation No road maintenance Low energy consumption Low maintenance costs Regenerative energy produced Minimal underground ventilation